Leading Diesel Engine Manufacturer: Precision Engineering and Innovation
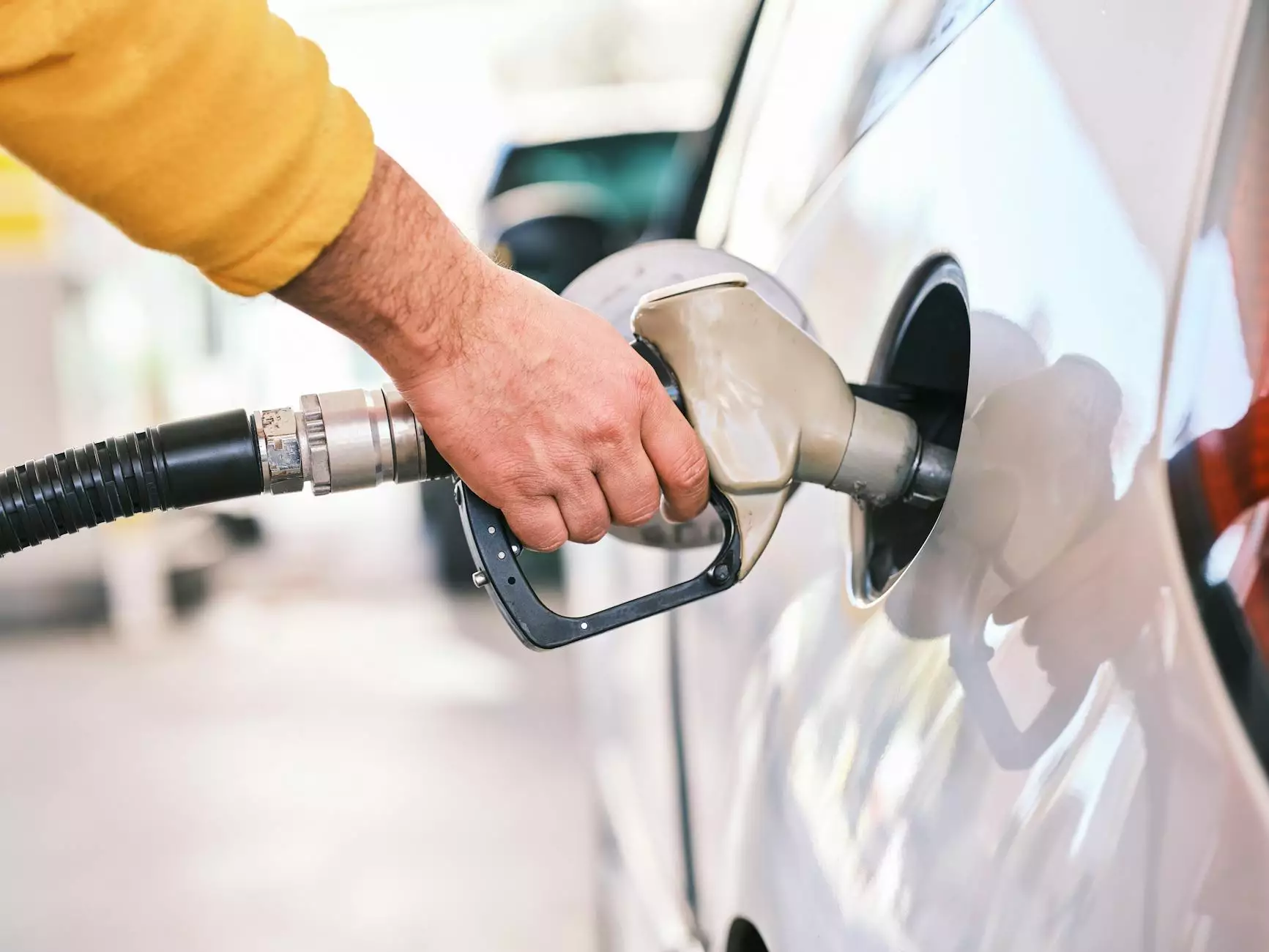
In the vast landscape of industrial machinery, the role of a diesel engine manufacturer cannot be overstated. Diesel engines are the backbone of many industries, powering everything from heavy machinery to generators, and their importance cannot be overlooked. This article delves into the intricate world of diesel engine manufacturing, exploring the innovations, benefits, and what to look for when choosing a manufacturer.
The Evolution of Diesel Engine Manufacturing
The genesis of diesel engines traces back to the late 19th century when Rudolf Diesel introduced an engine that promised greater efficiency and power. Over the decades, the diesel engine manufacturer sector has undergone profound transformations driven by technological advancements and the rising demand for efficient energy solutions.
Key Milestones in Diesel Engine Technology
- 1900s: The inception of diesel engines designed for industrial and commercial applications.
- 1940s-1950s: The expansion of diesel engines into transportation, particularly in trucking and marine applications.
- 1970s: The introduction of turbocharging technology, improving power output and efficiency significantly.
- 2000s: Emergence of modern electronic control units (ECUs), enhancing performance, fuel efficiency, and emissions control.
The Manufacturing Process of Diesel Engines
Creating a high-quality diesel engine involves a meticulous process that integrates advanced engineering, precision manufacturing, and stringent quality controls. The lifecycle of diesel engine manufacturing can be broadly divided into several stages:
1. Design and Engineering
The initial phase involves designing the engine to meet specific power, efficiency, and emissions standards. Engineers utilize advanced software for computational fluid dynamics (CFD) simulation, which helps in optimizing engine design for performance and fuel efficiency.
2. Material Selection
Choosing the right materials is crucial for durability and performance. Common materials utilized in diesel engine manufacturing include:
- Cast Iron: Used for engine blocks because of its strength and ability to withstand high-pressure conditions.
- Aluminum: Often used in components like cylinder heads for its lightweight and thermal conductivity properties.
- Steel: Used for crankshafts and other high-stress components due to its high tensile strength.
3. Precision Machining
The manufacturing process involves sophisticated machining techniques to create engine components. This includes:
- CNC Machining: Allows for high precision in manufacturing parts like pistons and camshafts.
- Grinding and Honing: Used to achieve the final surface finishes required for tight tolerances.
4. Assembly
Once all components are manufactured, the assembly process begins. Skilled technicians meticulously assemble the diesel engines, integrating each component with care to ensure optimal performance.
5. Testing and Quality Assurance
This stage is vital. Each diesel engine undergoes extensive testing to ensure it meets performance standards and regulatory compliance. This includes:
- Bench Testing: Evaluating engine parameters like power, torque, and efficiency.
- Emissions Testing: Ensuring compliance with environmental regulations.
Why Choose a Recognized Diesel Engine Manufacturer
Selecting the right diesel engine manufacturer is paramount for ensuring reliability, performance, and long-term satisfaction. Here are several considerations:
1. Reputation and Experience
A manufacturer with a long-standing reputation and extensive experience is more likely to produce durable engines. Companies that have survived market fluctuations and adapted to changing technologies usually incorporate the best practices in engine manufacturing.
2. Research and Development
Investing in R&D is essential for innovation. Leading manufacturers continually improve their products through the latest technologies, leading to enhanced performance and efficiency. Choosing a manufacturer with a strong R&D background ensures you acquire the latest advancements in diesel engine technology.
3. Customer Support and Service
Reliable post-purchase support is a critical factor. A good diesel engine manufacturer offers comprehensive customer service, including maintenance and support services, ensuring your engine operates optimally throughout its lifespan.
4. Warranty and Reliability
A robust warranty indicates a manufacturer’s confidence in their product quality. Look for manufacturers who offer comprehensive warranties on their diesel engines, as this reflects their commitment to durability and customer satisfaction.
Applications of Diesel Engines
The versatility of diesel engines is one of their standout features. They find applications across numerous sectors, including:
1. Transportation
Diesel engines power a large portion of the world’s heavy trucks and transport vehicles. Their fuel efficiency and durability make them ideal for long-haul transportation.
2. Construction
In the construction industry, diesel engines drive equipment such as excavators, bulldozers, and cranes, where high torque and durability are essential.
3. Agriculture
Farm machinery, including tractors and combines, typically relies on diesel engines, which offer the necessary power for demanding agricultural tasks.
4. Electricity Generation
Diesel generators are critical in remote locations where electricity is not readily available. They provide reliable power for various applications, from residential use to large-scale industrial operations.
5. Marine Applications
Many vessels utilize diesel engines for propulsion, given their high energy density and reliability over long distances in maritime environments.
Environmental Considerations and Innovations
As environmental regulations tighten globally, diesel engine manufacturers are innovating to produce cleaner emissions. Technologies such as selective catalytic reduction (SCR) and diesel particulate filters (DPF) are now common in modern diesel engines, significantly reducing pollution.
1. Emission Control Technologies
Leading manufacturers are investing in advanced emission control technologies, ensuring that their engines comply with stringent regulations while maintaining performance. This commitment to sustainability not only benefits the environment but also enhances the manufacturer’s reputation.
2. Alternative Fuels
With the push towards sustainability, many manufacturers are exploring alternative fuels that can be used in diesel engines, including biodiesel and synthetic fuels. This diversification can reduce reliance on traditional fossil fuels and promote greener operations.
Conclusion
In summary, the role of a diesel engine manufacturer is pivotal in various industrial sectors, from transportation to energy generation. Selecting the right manufacturer can have long-term implications for performance, efficiency, and operational costs. By considering aspects such as innovation, customer service, and sustainability, businesses can ensure that they partner with a manufacturer that aligns with their needs and values.
Choosing a leading diesel engine manufacturer like engine-family.com not only guarantees quality and reliability but also positions businesses to thrive in an ever-evolving marketplace.